Inhaltsverzeichnis:
Projektziel: 3D-Drucker kostengünstig in eine CNC-Fräse umbauen
Projektziel: 3D-Drucker kostengünstig in eine CNC-Fräse umbauen
Das Hauptziel dieses Projekts ist es, aus einem vorhandenen 3D-Drucker eine funktionstüchtige CNC-Fräse zu machen, ohne dabei tief in die Tasche greifen zu müssen. Der Fokus liegt darauf, die vorhandene Mechanik und Elektronik des Druckers maximal auszunutzen und so wenig wie möglich neu anzuschaffen. Dabei soll die Umrüstung so gestaltet werden, dass sie reversibel bleibt – also jederzeit zurückgebaut werden kann, falls der Drucker wieder für den ursprünglichen Zweck genutzt werden soll.
Im Zentrum steht die Integration eines Multifunktionswerkzeugs, etwa eines Dremels, als Fräseinheit. Die Steuerung erfolgt weiterhin über die bestehende Elektronik des 3D-Druckers, sodass keine teure CNC-Steuerung angeschafft werden muss. Ziel ist es, mit einfachen Anpassungen und leicht verfügbaren Bauteilen eine Lösung zu schaffen, die für Gravuren, leichte Fräsarbeiten und DIY-Projekte ausreicht.
Der Umbau richtet sich besonders an Bastler, die einen älteren oder defekten 3D-Drucker besitzen und diesen sinnvoll weiterverwenden möchten. Die Möglichkeit, vorhandene 3D-gedruckte Teile für Halterungen und Befestigungen einzusetzen, sorgt für Flexibilität und spart zusätzliche Kosten. Am Ende steht eine Maschine, die zwar nicht mit professionellen CNC-Fräsen konkurriert, aber für viele Anwendungen im Hobbybereich absolut ausreicht – und das zu einem Bruchteil der üblichen Kosten.
Erforderliche Hardware: Diese Komponenten benötigen Sie für den Umbau
Erforderliche Hardware: Diese Komponenten benötigen Sie für den Umbau
- Multifunktionswerkzeug (z. B. Dremel): Als Fräsmotor eignet sich ein handelsübliches Multifunktionswerkzeug mit variabler Drehzahl. Die flexible Welle ist optional, aber praktisch für schwer zugängliche Stellen.
- 3D-gedruckte Werkzeughalterung: Für die sichere Befestigung des Fräswerkzeugs am Druckerkopf ist eine maßgeschneiderte Halterung nötig. STL-Dateien für viele Druckermodelle finden sich auf Maker-Plattformen.
- Geeignete Fräser: Je nach Material kommen unterschiedliche Schaftfräser zum Einsatz. Für Holz und Kunststoff reichen einfache HSS- oder Hartmetallfräser.
- Frästisch oder Arbeitsplatte: Eine stabile, flache Unterlage (z. B. aus MDF oder Multiplex) dient als Arbeitsfläche und kann auf dem Druckbett fixiert werden.
- Befestigungsmaterial: Schrauben, Muttern und ggf. Federn oder Rändelmuttern sorgen für sicheren Halt von Frästisch und Werkstück.
- Kontaktplatte für Z-Homing: Eine kleine Metallplatte mit Kabel ermöglicht präzises Referenzieren der Z-Achse beim Werkzeugwechsel.
- Endstop-Erweiterungen: Je nach Druckermodell kann ein zusätzlicher Endschalter oder ein modifizierter Kontakt sinnvoll sein.
- Schutzmaßnahmen: Einfache Abdeckungen oder Schutzbrillen sind ratsam, um sich vor Staub und Spänen zu schützen.
Wer mag, ergänzt das Setup mit einem Not-Aus-Schalter oder einer Staubabsaugung. Das ist zwar kein Muss, aber definitiv ein Pluspunkt für Sicherheit und Komfort beim Fräsen.
Vorteile und Nachteile beim Umbau eines 3D-Druckers zur CNC-Fräse
Pro | Contra |
---|---|
Kostengünstige Nutzung vorhandener Hardware | Mechanik vieler 3D-Drucker ist für Fräskräfte nur bedingt ausgelegt |
Reversibel: Rückbau zum 3D-Drucker jederzeit möglich | Umbau und Rückbau bedeuten manuellen Aufwand |
Flexibler Einsatz: Gravieren, leichte Fräsarbeiten, DIY-Projekte | Leistungsgrenzen bei härteren Materialien wie Metall |
Verwendung günstiger, 3D-gedruckter Halterungen und Adapter | 3D-gedruckte Halterungen bieten begrenzte Stabilität |
Nutzung der bestehenden Elektronik, keine teure CNC-Steuerung nötig | Firmware-Anpassungen erforderlich, nicht immer trivial |
Große Unterstützung durch Maker-Community und offene Ressourcen | Erfordert Einarbeitung in Software und Maschinensteuerung |
Guter Einstieg zum Erlernen von CAM-Software und Frästechniken | Höherer Verschleiß bei häufigem Wechsel zwischen Druck- und Fräsbetrieb |
Möglichkeit, alte oder defekte 3D-Drucker sinnvoll weiterzuverwenden | Kein Ersatz für eine professionelle CNC-Fräse hinsichtlich Präzision und Durchsatz |
Vorbereitung: Ausbau des Extruders und Anpassung der Druckermechanik
Vorbereitung: Ausbau des Extruders und Anpassung der Druckermechanik
Bevor es ans Eingemachte geht, muss der Extruder samt Hotend entfernt werden. Das schafft Platz für die neue Fräseinheit und verhindert, dass Bauteile im Weg sind oder beschädigt werden. Schrauben Sie den Extruder vorsichtig ab und legen Sie alle Teile beiseite – wer weiß, vielleicht braucht man sie später noch einmal.
- Kabelmanagement: Sichern Sie lose Kabel mit Kabelbindern oder Klebeband, damit sie nicht in die Mechanik geraten. Besonders die Heizungs- und Temperatursensorleitungen sollten sauber verstaut werden.
- Führungsschlitten prüfen: Kontrollieren Sie, ob der Schlitten nach dem Ausbau des Extruders stabil bleibt. Falls nötig, können Abstandshalter oder zusätzliche Schrauben für mehr Halt sorgen.
- Gewichtsausgleich: Da der Fräsmotor meist schwerer ist als das ursprüngliche Hotend, kann ein Ausgleich durch kleine Gegengewichte oder eine Anpassung der Federspannung an der Z-Achse sinnvoll sein.
- Mechanische Endstops: Überprüfen Sie, ob die Endschalter noch korrekt ausgelöst werden. Manchmal ist eine kleine Nachjustierung nötig, damit die Referenzfahrt zuverlässig funktioniert.
Jetzt ist der Drucker bereit für den nächsten Schritt. Die Mechanik ist frei, die Achsen laufen leicht – und das Bastlerherz schlägt ein bisschen schneller, weil es gleich richtig losgeht.
Werkzeughalterung für den Fräskopf: Montage und Befestigung eines Dremels
Werkzeughalterung für den Fräskopf: Montage und Befestigung eines Dremels
Die Befestigung des Dremels am Druckerkopf ist ein kritischer Schritt, der über Stabilität und Präzision beim Fräsen entscheidet. Eine wackelige Konstruktion? Lieber nicht! Setzen Sie auf eine maßgeschneiderte Halterung, die exakt zu Ihrem Druckermodell und Werkzeugdurchmesser passt. 3D-gedruckte Adapter bieten sich hier besonders an, weil sie individuell anpassbar sind und sich leicht nachjustieren lassen.
- Maß nehmen: Vor dem Druck der Halterung unbedingt den Durchmesser des Dremels und die Befestigungspunkte am Schlitten exakt ausmessen. Ungenauigkeiten führen später zu Vibrationen oder gar Ausreißern beim Fräsen.
- Materialwahl: Für die Halterung eignet sich PETG oder ABS besser als PLA, da diese Kunststoffe weniger spröde sind und Vibrationen besser abfangen.
- Montage: Die Halterung wird mit Schrauben und Muttern am Schlitten befestigt. Ziehen Sie alles handfest an, aber überdrehen Sie die Gewinde nicht – sonst droht Bruchgefahr.
- Dremel einsetzen: Der Dremel wird in die Halterung geschoben und mit Klemmschrauben oder Schnellspannern fixiert. Achten Sie darauf, dass das Werkzeug nicht verrutschen kann, selbst wenn es mal ordentlich ruckelt.
- Testlauf: Nach der Montage lohnt sich ein kurzer Probelauf ohne Fräser, um zu prüfen, ob alles sicher sitzt und der Dremel frei läuft. Klappert oder wackelt etwas? Dann besser nochmal nachziehen oder die Halterung überarbeiten.
Wer auf Nummer sicher gehen will, kann zusätzlich dünne Moosgummistreifen zwischen Halterung und Werkzeug legen – das dämpft Vibrationen und schont die Lager. Mit einer soliden Befestigung steht dem ersten Fräsversuch nichts mehr im Weg.
Bau des Frästisches: Sichere Fixierung und Vorbereitung der Arbeitsfläche
Bau des Frästisches: Sichere Fixierung und Vorbereitung der Arbeitsfläche
Für präzise Fräsergebnisse braucht es eine absolut stabile Arbeitsfläche. Wackelt hier etwas, leidet sofort die Qualität. Eine MDF- oder Multiplexplatte mit mindestens 10 mm Stärke eignet sich als Frästisch besonders gut. Diese Platte wird direkt auf das Druckbett gelegt oder, falls möglich, mit den vorhandenen Schrauben und Federn fest verschraubt. So bleibt alles an Ort und Stelle, selbst wenn der Fräsmotor ordentlich Gas gibt.
- Bohrungen für Befestigung: Vor dem Einbau sollten passende Löcher in die Platte gebohrt werden, um sie mit den originalen Druckbettverschraubungen zu fixieren. Alternativ sorgen Klemmen oder Rändelmuttern für sicheren Halt.
- Werkstückaufnahme: Für wechselnde Projekte lohnt es sich, T-Nuten oder Einschlagmuttern in die Platte einzulassen. So lassen sich Werkstücke flexibel und wiederholgenau befestigen, ohne ständig neue Löcher bohren zu müssen.
- Oberflächenschutz: Ein dünnes Opferbrett aus Sperrholz oder HDF schützt den eigentlichen Frästisch vor unbeabsichtigten Durchfräsungen. Dieses kann einfach mit doppelseitigem Klebeband aufgebracht werden.
- Planheit prüfen: Mit einem Lineal oder einer Messuhr sollte die Oberfläche auf Ebenheit kontrolliert werden. Schon kleine Unebenheiten können zu unsauberen Fräsergebnissen führen.
Mit diesen Maßnahmen bleibt die Arbeitsfläche fest, plan und vielseitig nutzbar – ein echter Gamechanger für saubere und wiederholbare Fräsarbeiten.
Anpassungen an Endstops und Homing für präzises Arbeiten
Anpassungen an Endstops und Homing für präzises Arbeiten
Für exakte Fräsergebnisse muss das Homing-Verhalten des Druckers angepasst werden. Da der Werkzeugwechsel und die neue Fräslänge die Z-Referenz beeinflussen, ist eine zuverlässige Nullpunktbestimmung Pflicht. Besonders praktisch: eine leitfähige Kontaktplatte, die als Z-Probe dient. Diese wird auf dem Frästisch platziert und mit einem Kabel an den Endstop-Eingang angeschlossen. Sobald der Fräser die Platte berührt, erkennt die Steuerung den genauen Z-Nullpunkt.
- Firmware-Einstellungen: In der Firmware sollte der Z-Probe-Modus aktiviert und die Schaltlogik auf den neuen Kontakt angepasst werden. Das verhindert Fehlmessungen und sorgt für reproduzierbare Ergebnisse.
- Position der Endstops: Prüfen Sie, ob die Endschalter durch die neue Halterung oder den Fräsmotor blockiert werden. Falls nötig, versetzen Sie die Endstops oder nutzen Sie magnetische Alternativen, um weiterhin präzise Referenzfahrten zu ermöglichen.
- Automatisiertes Homing: Mit einem kleinen Makro im Start-G-Code kann das Werkzeug automatisch auf die Kontaktplatte fahren und den Nullpunkt bestimmen. Das spart Zeit und minimiert Fehlerquellen.
- Sicherheitsabstand: Nach dem Homing empfiehlt sich ein kleiner Sicherheitsabstand zur Platte, damit der Fräser beim Start nicht direkt ins Material eintaucht.
Mit diesen Anpassungen läuft das Homing zuverlässig und präzise – ein Muss, wenn aus dem 3D-Drucker eine brauchbare CNC-Fräse werden soll.
Firmware- und Softwareanpassung: 3D-Drucker auf CNC-Betrieb umrüsten
Firmware- und Softwareanpassung: 3D-Drucker auf CNC-Betrieb umrüsten
Damit der umgebaute 3D-Drucker CNC-Befehle korrekt verarbeitet, sind gezielte Anpassungen an Firmware und Software erforderlich. Zunächst sollte die Drucker-Firmware (häufig Marlin) so konfiguriert werden, dass sie ohne Heizbett- und Hotendüberwachung funktioniert. Andernfalls verweigert das System den Start, weil es keine Temperaturwerte mehr erhält.
- Thermal Runaway Protection deaktivieren: In der Konfigurationsdatei der Firmware müssen alle Temperaturüberwachungen abgeschaltet werden. Dies geschieht meist durch Auskommentieren oder Setzen entsprechender Flags.
- CNC-spezifische G-Code-Befehle aktivieren: Aktivieren Sie in der Firmware den CNC-Modus, sofern verfügbar. Dadurch werden Funktionen wie Spindelsteuerung und Werkzeugwechsel unterstützt.
- Firmware-Upload: Nach den Änderungen ist ein erneutes Flashen der Firmware notwendig. Prüfen Sie, ob der Drucker nach dem Neustart ohne Temperaturwarnungen hochfährt.
- CAM-Software wählen: Für die Erstellung der Fräsdaten empfiehlt sich eine leicht verständliche CAM-Software wie Estlcam oder FreeCAD Path. Diese Programme erzeugen CNC-tauglichen G-Code, der mit den meisten 3D-Drucker-Boards kompatibel ist.
- G-Code-Anpassungen: Entfernen Sie im generierten G-Code alle Befehle, die auf Extruder oder Heizbett abzielen. Stattdessen sollten Start- und Endsequenzen für CNC-Betrieb eingefügt werden, etwa das Aktivieren der Spindel oder das sichere Anheben der Z-Achse nach dem Fräsen.
- Speicherkarte oder USB: Übertragen Sie den angepassten G-Code wie gewohnt per SD-Karte oder USB-Kabel an den Drucker. Die meisten Boards akzeptieren CNC-G-Code ohne weitere Modifikationen.
Ein letzter Tipp: Testen Sie neue Einstellungen zunächst mit „Luftfräsen“, also ohne Material, um Fehlerquellen auszuschließen. So vermeiden Sie böse Überraschungen und schützen Maschine wie Werkstück.
Erstellung und Übertragung von Fräsdaten: Schritt-für-Schritt zum ersten CNC-Projekt
Erstellung und Übertragung von Fräsdaten: Schritt-für-Schritt zum ersten CNC-Projekt
Der Weg von der Idee zum gefrästen Werkstück beginnt mit der digitalen Vorbereitung. Zuerst wird das gewünschte Motiv oder Bauteil in einer CAD-Software entworfen. Für Einsteiger eignen sich Programme wie FreeCAD oder Fusion 360, da sie sowohl 2D- als auch 3D-Modelle unterstützen. Das fertige Design wird anschließend als DXF- oder STL-Datei exportiert.
Im nächsten Schritt wandert die Datei in eine CAM-Software, etwa Estlcam oder Candle. Hier definieren Sie die Fräsbahnen, legen Schnitttiefe, Vorschubgeschwindigkeit und Werkzeugdurchmesser fest. Besonders wichtig: Die Auswahl der Startpunkte und die Festlegung der Bearbeitungsreihenfolge, damit das Werkstück nicht verrutscht oder beschädigt wird.
- Simulation prüfen: Nutzen Sie die integrierte Vorschau, um den Fräsablauf virtuell zu kontrollieren. Fehler oder Kollisionen lassen sich so frühzeitig erkennen.
- G-Code exportieren: Nach der Freigabe der Fräsbahnen exportieren Sie den G-Code im Format, das Ihr 3D-Drucker versteht. Häufig ist dies ein Standard-G-Code ohne Extruderbefehle.
- G-Code anpassen: Fügen Sie falls nötig individuelle Start- und Endbefehle hinzu, etwa zum Aktivieren der Spindel oder Anheben der Z-Achse nach Abschluss.
- Übertragung: Speichern Sie den fertigen G-Code auf einer SD-Karte oder übertragen Sie ihn per USB-Kabel an den Drucker. Viele Geräte akzeptieren die Datei direkt, ohne weitere Konvertierung.
- Letzter Check: Überprüfen Sie, ob das Werkstück sicher fixiert ist und die Fräse korrekt eingerichtet wurde, bevor Sie den Startknopf drücken.
Mit dieser klaren Abfolge gelingt der Sprung vom digitalen Entwurf zum ersten gefrästen Objekt – und das ganz ohne Rätselraten oder Frust. Einfach ausprobieren, Schritt für Schritt!
Praxistipp: Sicheres Einrichten und Fixieren von Fräser und Werkstück
Praxistipp: Sicheres Einrichten und Fixieren von Fräser und Werkstück
Ein stabil montierter Fräser und ein fest fixiertes Werkstück sind das A und O für saubere Ergebnisse und Sicherheit. Schon kleine Nachlässigkeiten führen zu unschönen Vibrationen, Werkzeugbruch oder im schlimmsten Fall zu Verletzungen. Es lohnt sich, hier besonders sorgfältig zu arbeiten.
- Fräser einspannen: Setzen Sie den Fräser so tief wie nötig, aber so kurz wie möglich in die Spannzange ein. Je weniger Überstand, desto stabiler läuft das Werkzeug. Ziehen Sie die Spannzange mit dem passenden Schlüssel kräftig, aber gefühlvoll an – ein „Überdrehen“ kann das Werkzeug beschädigen.
- Werkstückbefestigung: Nutzen Sie je nach Material und Größe Schraubzwingen, T-Nuten, doppelseitiges Klebeband oder spezielle Niederhalter. Besonders bei kleinen Teilen ist ein zusätzlicher Anschlag sinnvoll, damit sich nichts verdreht oder verrutscht.
- Vorsicht bei dünnen Materialien: Legen Sie bei filigranen Werkstücken eine Opferplatte darunter, um ein Durchbrechen zu verhindern und die Unterlage zu schonen.
- Letzter Sicherheitscheck: Drehen Sie die Spindel vor dem Start einmal per Hand durch. So merken Sie sofort, ob irgendwo ein Kontakt besteht oder das Werkstück nicht frei liegt.
- Schutz für Augen und Hände: Tragen Sie immer eine Schutzbrille. Gerade bei kleinen Fräsern fliegen gerne mal Späne oder Splitter unkontrolliert durch die Gegend.
Mit diesen Kniffen läuft das Fräsen sicherer und die Ergebnisse überzeugen – ganz ohne böse Überraschungen.
Beispielprojekt: Fräsen eines Holzschilds mit einem modifizierten 3D-Drucker
Beispielprojekt: Fräsen eines Holzschilds mit einem modifizierten 3D-Drucker
Ein personalisiertes Holzschild ist das perfekte Einsteigerprojekt, um die Möglichkeiten des umgebauten 3D-Druckers als CNC-Fräse auszuloten. Hier eine kompakte Schritt-für-Schritt-Anleitung für ein gelungenes Ergebnis:
- Design-Auswahl: Erstellen Sie in einer CAD-Software ein einfaches Schild mit Schriftzug oder Motiv. Achten Sie darauf, dass die Linien nicht zu fein sind – ein Fräserdurchmesser von 2 mm ist ein guter Startpunkt.
- Materialwahl: Verwenden Sie gut zu bearbeitendes Holz wie Pappel oder Birke. Diese Hölzer splittern wenig und lassen sich sauber fräsen.
- Frässtrategie: Legen Sie in der CAM-Software eine Gravurstrategie fest, zum Beispiel eine Konturfräsung für den Schriftzug und eine Taschenfräsung für Flächen. Definieren Sie die Schnitttiefe so, dass das Schild stabil bleibt (z. B. 2–3 mm für Gravuren).
- Fräserauswahl: Ein V-Nutfräser sorgt für saubere, scharfe Gravuren. Für die Außenkontur empfiehlt sich ein gerader Schaftfräser.
- Vorschub und Drehzahl: Starten Sie mit moderaten Werten, etwa 500 mm/min Vorschub und mittlerer Drehzahl. Passen Sie die Parameter nach den ersten Testläufen an, um Ausrisse zu vermeiden.
- Nachbearbeitung: Nach dem Fräsen schleifen Sie die Oberfläche leicht an und entfernen eventuelle Grate. Ein Tropfen Holzöl oder Wachs hebt die Maserung hervor und schützt das Schild.
Mit diesem Projekt erhalten Sie nicht nur ein individuelles Ergebnis, sondern sammeln auch wertvolle Erfahrungen im Umgang mit Fräsparametern, Materialverhalten und der Nachbearbeitung. Wer mag, kann das Schild noch farbig gestalten oder mit Aufhängern versehen – der Kreativität sind keine Grenzen gesetzt.
Häufige Probleme und Lösungen beim Umbau
Häufige Probleme und Lösungen beim Umbau
- Unzureichende Steifigkeit der Achsen: Besonders bei älteren oder günstigen 3D-Druckern kann die Mechanik unter den höheren Kräften beim Fräsen nachgeben. Hier hilft es, Führungen und Lager auf Spiel zu prüfen und gegebenenfalls durch hochwertigere Linearlager oder zusätzliche Verstrebungen zu ersetzen.
- Vibrationen und Resonanzen: Tritt beim Fräsen ein unangenehmes Dröhnen auf, liegt das oft an schlecht entkoppelten Motoren oder lockeren Schraubverbindungen. Abhilfe schaffen Moosgummipads unter dem Frästisch, nachgezogene Schrauben und eine Reduzierung der Vorschubgeschwindigkeit.
- Überhitzung der Motortreiber: Da Fräsvorgänge meist länger dauern und die Achsen stärker belastet werden, können Motortreiber überhitzen. Ein kleiner Lüfter direkt auf die Treiberplatine oder ein Kühlkörper auf den Chips verlängert die Lebensdauer und verhindert Ausfälle.
- Unpassende Fräserlänge: Wird ein zu langer Fräser verwendet, kann dieser durchbiegen oder brechen. Am besten immer den kürzestmöglichen Fräser wählen, der für das Werkstück ausreicht.
- Unpräzise Z-Höhe nach Werkzeugwechsel: Wenn die Fräse nach einem Werkzeugwechsel nicht exakt auf die gleiche Höhe zurückkehrt, empfiehlt sich ein automatisiertes Z-Null-Setzen mit einer Kontaktplatte oder ein manuelles Nachjustieren mit einer Fühlerlehre.
- Staub- und Spanansammlungen: Ohne Absaugung kann sich schnell eine dicke Schicht Späne auf dem Frästisch bilden, die die Präzision beeinträchtigt. Ein kleiner Staubsauger oder eine einfache Bürstenleiste rund um den Fräser hält die Arbeitsfläche frei.
- Stromausfälle oder Unterbrechungen: Ein plötzlicher Stromausfall kann das Projekt ruinieren. Mit einer unterbrechungsfreien Stromversorgung (USV) bleibt die Steuerung aktiv, bis der Fräsvorgang sicher gestoppt werden kann.
Mit diesen Lösungen lassen sich typische Stolpersteine beim Umbau effektiv umgehen – und der Spaß am Fräsen bleibt erhalten.
Praktische Hinweise für Materialien, Schnittgeschwindigkeit und Ergebniskontrolle
Praktische Hinweise für Materialien, Schnittgeschwindigkeit und Ergebniskontrolle
- Materialauswahl: Für den Einstieg eignen sich weiche Hölzer wie Pappel, Kiefer oder Sperrholz, da sie die Mechanik weniger beanspruchen und saubere Schnittkanten ermöglichen. Kunststoffplatten (z. B. Acryl oder PVC) lassen sich ebenfalls gut bearbeiten, sofern der Fräser scharf ist und die Drehzahl angepasst wird. Bei härteren Materialien wie Aluminium ist äußerste Vorsicht geboten: Hier sind sehr geringe Zustellungen und spezielle Fräser notwendig, um Schäden an der Maschine zu vermeiden.
- Schnittgeschwindigkeit: Die optimale Geschwindigkeit hängt vom Material, Fräserdurchmesser und der Leistungsfähigkeit des Dremels ab. Als Faustregel gilt: Lieber langsam und mit mehreren Durchgängen arbeiten, statt zu viel Material auf einmal abzutragen. Für Holz empfiehlt sich ein Vorschub von 300–600 mm/min bei einer Schnitttiefe von 1–2 mm pro Durchgang. Bei Kunststoffen kann die Geschwindigkeit etwas reduziert werden, um ein Schmelzen zu verhindern. Testläufe an Reststücken helfen, die idealen Werte zu finden.
- Ergebniskontrolle: Nach jedem Fräsvorgang empfiehlt sich eine Sichtprüfung auf Ausrisse, Brandspuren oder Gratbildung. Eine Lupe oder ein Makro-Foto offenbart feine Details und mögliche Schwächen im Schnittbild. Wer es ganz genau wissen will, misst mit einer Schieblehre die Abweichung zur Sollkontur. Für wiederholbare Ergebnisse empfiehlt sich, die Fräser regelmäßig auf Schärfe zu prüfen und verschlissene Werkzeuge rechtzeitig zu ersetzen.
- Feinabstimmung: Kleine Anpassungen an Vorschub, Drehzahl und Schnitttiefe können einen enormen Unterschied machen. Notieren Sie erfolgreiche Einstellungen für jedes Material – so entsteht mit der Zeit eine persönliche Datenbank, die spätere Projekte erleichtert.
Zusätzliche Ressourcen: STL-Dateien, Anleitungen und Community-Tipps
Zusätzliche Ressourcen: STL-Dateien, Anleitungen und Community-Tipps
- STL-Dateien für Werkzeughalterungen: Auf Plattformen wie Thingiverse oder Printables finden sich zahlreiche kostenlose Modelle, die speziell für den Umbau von 3D-Druckern zu CNC-Fräsen entwickelt wurden. Suchen Sie gezielt nach Ihrem Druckermodell, um passgenaue Halterungen und Adapter zu erhalten.
- Detaillierte Schritt-für-Schritt-Anleitungen: Umfangreiche Tutorials mit Fotos und Videoanleitungen gibt es auf Instructables sowie in einschlägigen Maker-Blogs. Viele Anleitungen gehen auf spezielle Probleme einzelner Druckermodelle ein und bieten hilfreiche Praxistipps für Einsteiger.
- Community-Foren und Austausch: In Foren wie reprap.org, 3D-Druck-Community.de oder im Subreddit r/3Dprinting tauschen sich Bastler und Profis regelmäßig über ihre Erfahrungen aus. Hier erhalten Sie Antworten auf knifflige Fragen, Empfehlungen für CAM-Software und Hinweise zu optimalen Fräsparametern.
- Materialdatenbanken und Schnittwerttabellen: Spezielle Online-Ressourcen bieten Tabellen mit empfohlenen Schnittgeschwindigkeiten und Fräsertypen für verschiedene Materialien. Solche Datenbanken erleichtern die Auswahl der richtigen Einstellungen für Ihr Projekt.
- Open-Source-Firmware und G-Code-Beispiele: Github-Repositories enthalten häufig angepasste Firmware-Versionen und Beispiel-G-Code speziell für CNC-Umbauten. So lässt sich der Einstieg in die Softwarekonfiguration deutlich beschleunigen.
Wer sich inspirieren lassen möchte, findet auf YouTube zahlreiche Projektvideos, in denen Umbauten und Fräsarbeiten Schritt für Schritt dokumentiert werden. Der Austausch mit der Community ist oft Gold wert – gerade bei individuellen Herausforderungen oder kreativen Lösungen.
Fazit: So gelingt der Umbau eines 3D-Druckers zur CNC-Fräse
Fazit: So gelingt der Umbau eines 3D-Druckers zur CNC-Fräse
Der Umbau eines 3D-Druckers zur CNC-Fräse eröffnet überraschend viele Möglichkeiten, die weit über einfache Gravuren hinausgehen. Wer bereit ist, sich auf die Feinheiten der Mechanik und Elektronik einzulassen, kann mit überschaubarem Aufwand ein Werkzeug schaffen, das im Hobbybereich echte Präzision liefert. Besonders spannend: Durch die flexible Kombination von 3D-gedruckten Bauteilen und frei verfügbaren Softwarelösungen lassen sich individuelle Anpassungen nahezu endlos umsetzen.
- Experimentierfreude zahlt sich aus – gerade bei der Optimierung von Fräsparametern oder der Erweiterung um zusätzliche Features wie automatische Werkzeugvermessung.
- Die stetig wachsende Open-Source-Community bietet eine Fülle an Inspiration und Unterstützung, sodass auch ungewöhnliche Projekte realisierbar werden.
- Mit jedem neuen Werkstück wächst das Verständnis für Materialverhalten und Maschinensteuerung – ein echter Lerngewinn, der sich nicht nur auf das Fräsen beschränkt.
Wer sich auf den Prozess einlässt, profitiert nicht nur von günstigen Einstiegskosten, sondern entwickelt mit der Zeit eine persönliche Lösung, die exakt zu den eigenen Anforderungen passt. Damit wird aus einem ausgedienten 3D-Drucker ein vielseitiges Werkzeug, das im kreativen Alltag kaum noch wegzudenken ist.
Produkte zum Artikel
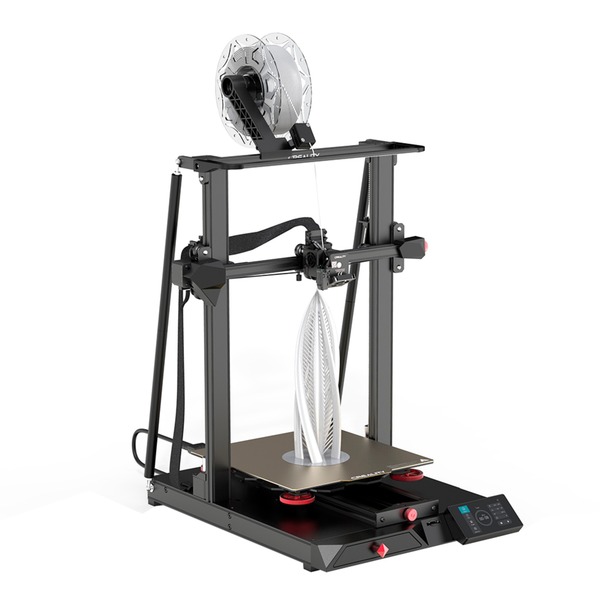
749.00 €* * inklusive 0% MwSt. / Preis kann abweichen, es gilt der Preis auf dem Onlineshop des Anbieters.
FAQ: 3D-Drucker einfach zur CNC-Fräse umbauen
Welche 3D-Drucker eignen sich für den Umbau zur CNC-Fräse?
Am besten eignen sich Standardmodelle wie der Ender 3 oder vergleichbare Kartesische 3D-Drucker mit stabilem Rahmen. Wichtig ist eine ausreichend robuste Mechanik, um den Fräskräften standzuhalten.
Welches Werkzeug wird als Fräsmotor verwendet?
Für den Umbau wird meist ein Dremel oder ein anderes Multifunktionswerkzeug mit variabler Drehzahl als Fräsmotor eingesetzt, das sich leicht mit einer passenden Halterung am Druckerkopf befestigen lässt.
Muss die Firmware des Druckers angepasst werden?
Ja, die Firmware (z. B. Marlin) sollte so konfiguriert werden, dass sie ohne Temperaturüberwachung und mit CNC-spezifischen Funktionen wie Spindelsteuerung und Werkzeuglängenausgleich arbeitet.
Welche Materialien lassen sich mit einem umgebauten 3D-Drucker fräsen?
Geeignet sind vor allem weiche Materialien wie Holz, Kunststoff oder Acryl. Für Metalle reicht die Stabilität und Motorleistung eines umgebauten 3D-Druckers normalerweise nicht aus.
Kann der Umbau wieder rückgängig gemacht werden?
Ja, der Umbau ist in der Regel komplett reversibel. Der Drucker kann jederzeit wieder zum 3D-Druckbetrieb zurückgebaut werden, da keine mechanischen Änderungen am Grundaufbau vorgenommen werden müssen.